塑料制品的着色可分为内着色和外着色两种。内着色是在塑料加工前的配料中加入着色剂,使制品内外有均匀的色泽。外着色是指采用诸如印刷、烫金、电镀、喷涂、贴花、真空蒸镀等仅在塑料表面着色的方法。本文所指的是内着色,它的目的不仅为了装饰塑料使它美观大方而且便于识别(电缆和包装),改善光学性能(照明灯具)、电性能(赋予导电性),提高机械强度和耐气候性等。
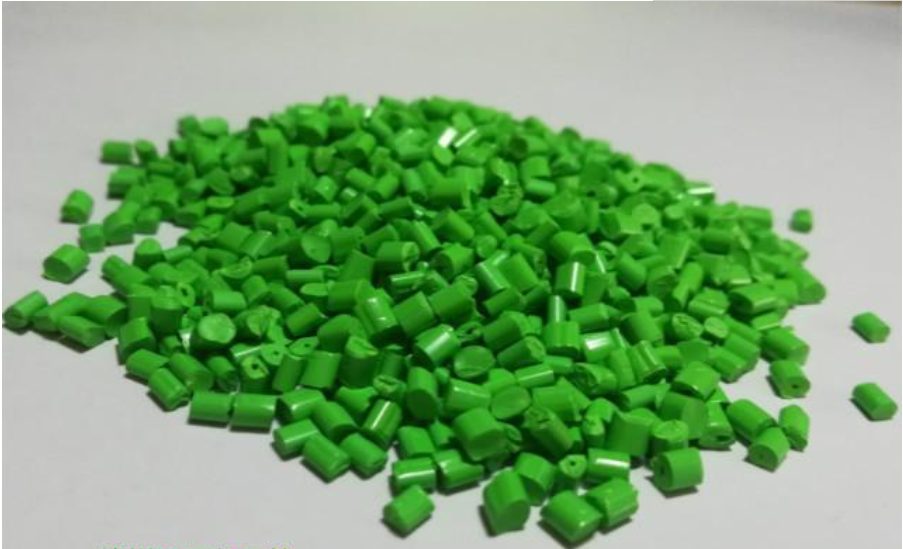
塑料内着色用的着色剂可分为染料和颜料两大类。染料是有强烈着色能力的有机化合物,它虽然有色彩鲜艳、色谱齐全、着色力大等优点,但它们的耐热、耐光、耐溶剂性一般不佳,易从塑料中渗出或迁移,因此印染工业中大量使用的水溶性染料一般都不适用于塑料,只有某些油溶性和醇溶性染料(如偶氮类、蒽醌类染料)在耐热性要求不高时方可使用,所以塑料工业中所用的着色剂主要是颜料,颜料可分为无机和有机的两种。无机颜料有热稳定性好、价格便宜的优点,但它的色泽缺乏光亮和透明性,而有机颜料的着色强度高,色彩鲜艳,但价格较高。
无机颜料主要有二氧化钛、氧化铁、氧化锌、铬酸盐、镉化物和汞镉等。其中二氧化碳是最广泛应用的白颜料,常与其他颜料相溶配得一系列色彩。它有化学惰性、热稳定性好、价格不贵、着色强度高等优点。有机颜料主要炭黑、偶氮颜料、酞花菁、喹哪酮、苝、异吲哚酮、蒽醌、硫靛及各种酸碱颜料,常见的有联苯胺黄、3132大红粉、金光红C、耐晒大红BBN、颜料红57:1、永固黄HR、永固黄2GS、永固桔黄G、酞菁蓝、酞菁绿等,炭黑是最普遍使用的黑颜料,它有价廉色牢、分散性好、流动性佳的优点,同时它还是赋予塑料导电性和防紫外线降解的良好填充剂。该选用何种颜料来着色,这在很大程度上取决于加工温度、塑料中其他添加剂的存在以及塑料制品的最终用途,但最需要考虑的是这种颜料的热稳定性能否承受一定的加工温度和时间。
塑料着色用的颜料添加量一般在1%以下,它对塑料制品机械强度的影响可不予考虑。但当颜料颗粒粗大、分散不良时会降低制品的抗冲击强度,由于锰、铁、钴、镍、铜等金属离子有促进聚氯乙烯热老化的作用,因此使用这类金属的颜料时要倍加注意。无机颜料通常对紫外线有遮蔽保护作用,而有机颜料对紫外线老化却又促进作用,因为它能吸收光能且把这部分能量转移给聚合物,须予注意。有机颜料有某种成核剂作用,因此对聚烯烃结晶型聚合物的成型收缩率有一定的影响。
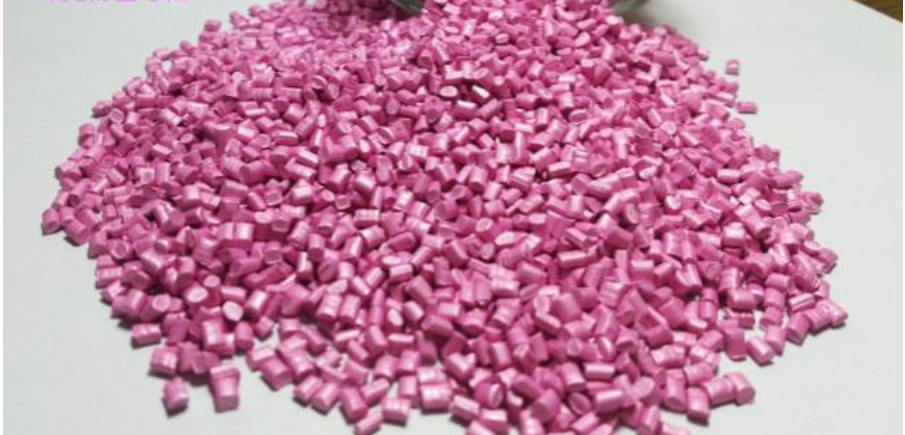
颜料对塑料大多是不溶的,它靠在塑料中分散成微粒状由表面遮盖作用而着色。颜料的着色强度或着色力是指将白色材料着色成某种色泽时所需用量,达到相同色泽时的颜料用量愈小则其着色力就愈大。像有机颜料中耐晒大红BBN、金光红C、联苯胺黄G、永固黄、艳红6B、永固桔黄G、酞菁蓝和酞菁绿G等都有色彩鲜艳、着色力高的特性。颜料的分散性对其着色力有很大的影响,而着色的均匀性与混合及加工设备的功效有关。细微的有机颜料颗粒在摩擦和高压下会结团成为压缩粒子,严重影响颜料的分散度、减弱着色力甚至降低塑料的机械强度,因此通常在有机颜料中加入某些无机填料如碳酸钙,起缓冲它在操作过程中的压缩成团作用。